20/12/2019
Construction of 1000 Soil Mixing columns on the Pont de Sèvres station worksite, part of Grand Paris Express work package T3A
After a summer marked by construction of an initial fibreglass-anchored diaphragm wall and a Berlin type-wall operation, the special works at the Pont de Sèvres station – part of Grand Paris Express work package T3A – have taken on a new dimension. Early autumn saw the start of Soil Mixing in front of the station box.
This phase of work involves the general upgrading of soils inside the future station to significantly increase the abutment in front of the diaphragm walls during earthworks operations. This is required because the station’s perimeter diaphragm wall (1.5 m thick and 45 m deep) which is firmly embedded in healthy chalk encounters a significant depth of decomposed chalk with poor geomechanical properties at between 15 and 39 m depth.
Subjected to high levels of soil and water pressure, the wall shows excessive distortion relative to sensitive adjoining structures during earthworks.
To ensure that these distortions are properly controlled, the contractor had formed 17 load-bearing separating walls in 1.5 m thick diaphragm wall for the full depth of the decomposed chalk (opposite each panel), which had to be crossed by the tunnel boring machine (TBM) prior to excavation of the station.
The Horizon consortium worked in partnership with consortium subcontractor Soletanche Bachy Fondations Spéciales (SBFS) and the Eurofrance design office to propose a technical adaptation involving the replacement of these load-bearing separating walls by a general Soil Mixing solution that would be cheaper and limit the risk of the tunnel boring machine becoming wedged.
To obtain approval for this solution, a test plot was carried out on site in March 2019, with the construction of 15 Soil Mixing columns and a major geotechnical testing campaign conducted using core samples taken from the centre of the treated material. The soil/cement mixture sampled is similar to a soil concrete with compressive strength results in the range of 3 to 6 MPa.
The successful test outcome meant that the solution could then be used on a much larger scale for this work site.
So the SBFS Fundex F5000 foundation drilling rig has been in residence on the banks of the Seine in Boulogne-Billancourt facing the Île Seguin since the end of October. The drilling rig is fitted with special tools specifically designed and built for this project under a collaborative project involving the plant and machinery teams of Soletanche Bachy and the manufacturer IHC. The rig has twin rotary heads driving two drill shafts fitted with 11 m long mixing blades on the lower section. So each time the rig is positioned, it drills two slightly secant 1.5 m diameter columns 39 m deep.
The bentonite/cement grout mixture is injected from the bottom at a depth of 15 m (the point of entry into the chalk) via the hollow core of the drill shafts. Throughout the column forming process, the drilling rig is supplied by two concrete pumps fed directly from the grouting plant. The plant is designed to deliver 560 kg/m3 (0.7 water-to-cement ratio) of cement slurry at a flow rate of 80 m3/hr. To achieve this specification, a modular digester produces a stock of slurry stored in a swimming pool and two Moritz 3000s feed the cement on demand. The entire system is supplied with water pumped from the Seine.
Drilling operations are carried out by adding compressed air to the tool line, and monitored by a deflection sensor at the tip of the auger. The machine’s onboard computer also checks that the soil mix is correct and directly verifies the degree of penetration into the healthy chalk using an anchoring criterion. The result is that the depth of soil treatment is optimised for each pair of drillings.
The data are then uploaded to the new Zetta-Lyze online application for continuous processing by the on-site team. Drill logs and 3D models of column deviations are therefore available virtually in real time.
After a period of adjustment and ramp-up, the two shifts of the team hit their stride to drill between 8 and 14 pairs (28 columns) per day. This excellent level of productivity was made possible by the meticulous preparatory work which involved many different parts of the company (SBFS, of course, but also the plant and machinery design office, materials laboratory, Group technical department and experts, the Eurofrance design office and the T3A site team).
In total, 504 slightly secant twin shafts will be drilled and filled to build 1008 columns by February 2020.
Immediately after the Soil Mixing operation, the diaphragm wall teams working on the station’s adjoining connecting corridor will take over to create the station’s diaphragm wall. Three KS buckets organised in three different work positions are planned as part of this work in spring 2020. Lastly, the joint between the containment diaphragm wall and the Soil Mixing columns will be bonded using jet grouting.
From that point onwards, the station will be ready to allow the tunnel boring machine to pass through having started its excavation from the launch shaft in January 2020.
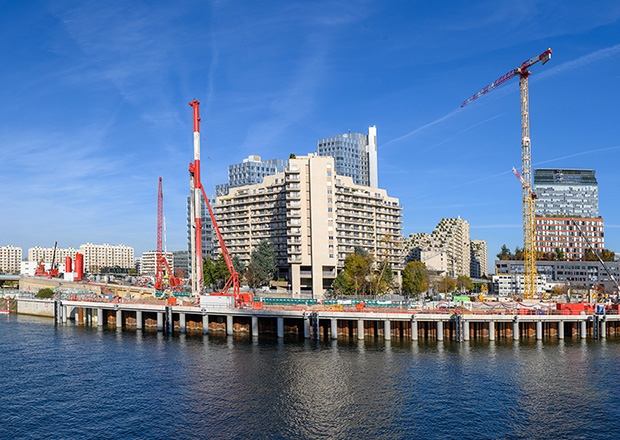